Essential Methods for Testing of Plastics: From Strength to Sustainability
Plastics have become indispensable in modern industries, ranging from packaging and electronics to automotive and medical devices. As their applications continue to expand, the need for thorough and reliable testing has become more critical than ever. Ensuring that plastics meet performance, safety, and sustainability standards requires the use of sophisticated testing methods that assess everything from strength to environmental impact.
In this blog, we will discuss the essential methods for testing plastics to ensure they meet the necessary requirements for durability, safety, and sustainability.
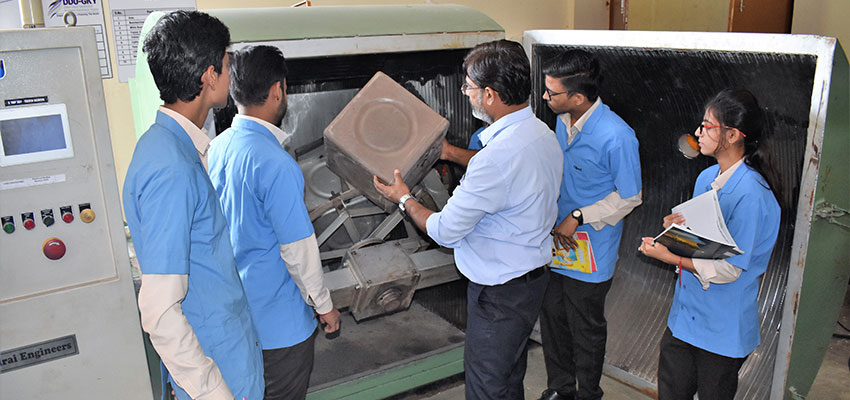
The Importance of Comprehensive Plastic Testing
Plastic materials must undergo various tests to assess their performance under different conditions. These tests ensure the plastic’s ability to perform in its intended application, from withstanding physical stress to complying with environmental regulations.
Ensuring Durability and Performance
Durability is a key requirement for plastics, especially in industries where long-term performance is essential, such as automotive and construction. Testing allows manufacturers to evaluate how well plastics hold up under mechanical stress, temperature variations, and exposure to chemicals.
Supporting Sustainability and Compliance
With global environmental regulations becoming more stringent, plastics must not only perform well but also comply with sustainability standards. Testing helps manufacturers determine whether their products meet regulatory requirements like REACH and RoHS, which limit the use of hazardous substances and promote environmentally friendly materials.
Essential Methods for Testing Plastics
To ensure that plastics meet durability and sustainability standards, they undergo a series of critical tests. These tests evaluate key properties such as strength, thermal resistance, chemical compatibility, and environmental impact.
1. Tensile Strength Testing
Tensile strength testing is one of the most commonly used methods for determining the mechanical properties of plastics. This test measures a plastic's ability to resist being pulled apart, providing crucial data on its strength and flexibility. During the test, a plastic specimen is subjected to a controlled tension until it breaks.
Key Parameters from Tensile Testing
- Tensile Strength at Break: The maximum stress a material can withstand before breaking.
- Elongation at Break: The percentage increase in length before the material breaks, indicating its flexibility.
- Modulus of Elasticity: A measure of the material’s stiffness, important for rigid applications like automotive components.
2. Impact Resistance Testing
Plastics used in applications where they may experience sudden shocks or collisions must undergo impact resistance testing. This method measures how much energy a material can absorb before it fractures. Impact tests are critical for materials used in protective gear, packaging, and automotive parts.
Common Impact Tests
- Izod Impact Test: Measures the material’s ability to resist impact from a swinging pendulum.
- Charpy Impact Test: Similar to the Izod test, but it evaluates how much energy the material can absorb before fracturing.
3. Thermal Analysis
Plastics are often exposed to fluctuating temperatures, making it essential to assess their thermal properties. Thermal analysis methods help determine a plastic’s ability to withstand high temperatures without deforming or losing its structural integrity.
Heat Deflection Temperature (HDT)
The HDT test measures the temperature at which a plastic material begins to deform under a specific load. This is essential for applications where plastics must retain their shape and strength under heat, such as in automotive engine parts or electronic casings.
Differential Scanning Calorimetry (DSC)
DSC is used to measure the thermal transitions of plastics, such as melting points and glass transition temperatures. This helps manufacturers choose materials that remain stable under operational temperatures, especially for medical devices and industrial equipment.
4. Chemical Resistance Testing
In industries where plastics are exposed to chemicals, testing their chemical resistance is crucial. Chemical resistance testing evaluates how a plastic reacts when exposed to substances like solvents, oils, or acids. This test ensures that the plastic can maintain its performance without degrading or corroding over time.
Importance of Chemical Resistance
- Longevity: Chemical resistance testing helps determine the lifespan of plastics in harsh chemical environments.
- Safety: For applications like food packaging or medical devices, chemical resistance ensures that plastics will not leach harmful substances when exposed to other chemicals.
5. Environmental Stress Cracking (ESC) Testing
Environmental stress cracking is one of the leading causes of plastic failure. ESC testing simulates real-world conditions where plastics are exposed to mechanical stress and chemicals. This test identifies how likely a plastic is to crack when subjected to stressors such as UV radiation, temperature fluctuations, or chemical exposure.
Real-World Applications of ESC Testing
- Outdoor Equipment: Ensures that plastics used in outdoor environments can withstand exposure to the elements without cracking.
- Chemical Containers: Verifies that containers made from plastic materials will not crack or fail when exposed to chemicals under pressure.
6. Flammability Testing
Flammability testing evaluates the fire resistance of plastics, ensuring they meet safety regulations, especially for materials used in construction, electronics, and transportation. This test measures how easily a material ignites, its burning rate, and whether it produces flaming drips.
UL 94 Flammability Standard
The UL 94 test classifies plastics based on their flame-retardant properties. Materials that meet this standard are often used in electrical applications, ensuring they can resist combustion and protect users from fire hazards.
7. Biodegradability and Environmental Impact Testing
In response to growing environmental concerns, testing the biodegradability of plastics is essential for ensuring they align with sustainability goals. Biodegradability tests determine how long it takes for plastics to break down under natural conditions, which is crucial for reducing landfill waste and marine pollution.
Importance of Environmental Testing
- Compliance with Regulations: Ensures that plastics meet environmental laws such as REACH and RoHS.
- Sustainability: Helps manufacturers create products that contribute to the circular economy, reducing the environmental impact of plastic waste.
Compliance with Industry Standards
To meet both durability and sustainability requirements, plastics must comply with international standards set by organizations such as ISO and ASTM. These standards specify the testing methods, performance criteria, and safety measures required for plastics used in various industries.
ISO and ASTM Standards for Plastics
- ISO 527: Specifies the tensile properties of plastics and is essential for evaluating strength and flexibility.
- ASTM D638: Describes the method for tensile testing of plastics, ensuring uniformity and accuracy in testing.
- ISO 11357: Covers thermal analysis methods like DSC and HDT, used to determine the heat resistance of plastics.
Sustainability and Compliance with REACH and RoHS
For manufacturers looking to align with global sustainability efforts, compliance with REACH and RoHS is critical. These regulations restrict the use of hazardous substances and ensure that plastics do not pose environmental or health risks.
Advanced Testing Technologies
As technology advances, testing methods have evolved to become more efficient, accurate, and comprehensive. Non-destructive testing (NDT) and automated testing systems are examples of innovations that allow manufacturers to test plastics more effectively while reducing costs and time.
Non-Destructive Testing (NDT)
NDT methods like ultrasonic and X-ray testing allow manufacturers to inspect the internal structure of plastics without damaging them. These methods help identify defects such as voids or internal cracks that could compromise the material’s durability.
Automated Testing Systems
Automated systems streamline the testing process by allowing large quantities of plastics to be tested with minimal manual intervention. This not only improves efficiency but also ensures consistent and accurate results.
Conclusion: A Holistic Approach to Plastic Testing
Ensuring the durability and sustainability of plastics requires a comprehensive approach to testing. By using a range of methods, from tensile strength to biodegradability testing, manufacturers can guarantee that their products meet both performance and environmental standards.
In a world that increasingly values sustainability and compliance, thorough testing of plastics is not just a technical necessity—it’s an essential part of creating reliable, safe, and eco-friendly products.